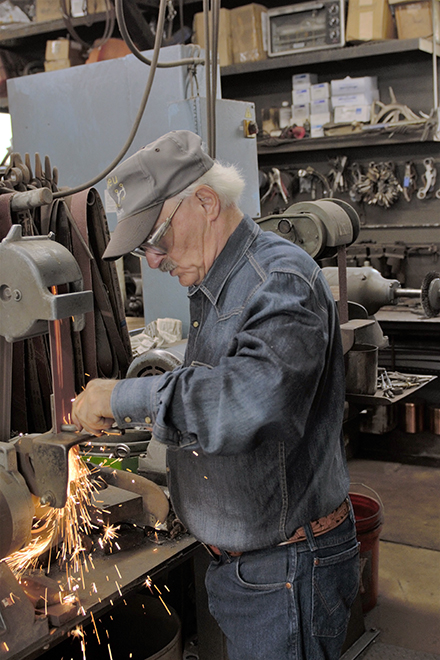
The smell of burning metal hangs in the air. It’s so thick you can taste it – it’s that same metallic flavor you get when you bite your tongue and it bleeds. According to Nobel Prize in Medicine scientists, metal doesn’t have a scent. Doctors Linda Burck and Richard Axel discovered the genes that determine a person’s smell and their work says the odor “perceived as metallic are really by-products of the metals reacting with skin or impurities in the metal itself.”
But when you’re standing in a 50 by 24-foot workshop with enough steel to make 1,000 bridles hanging on just one wall, it’s hard to believe that what you’re smelling isn’t coming from the metal itself. Pawling, New York custom bit and spur maker Ray Maheu and employee Dave Parthemore are oblivious to the scent. They’ve each been metal workers for decades. Even Maheu’s wife, Candy, has grown accustomed to the scent, but she marvels at noticing something different in the shop every day.
“I always see something new whenever I walk in here,” she said. “It’s kind of amazing that after 31 years there’s still something new I’m noticing every day. That’s what makes this so much fun.”
It’s easy to understand how Candy, who is in and out of the shop multiple times a day, can say that. There’s seemingly a larger variety (and quantity of tools) than at the local Home Depot. Shanks of varying sizes and lengths hang from a peg board below the sole window in the shop. Mouthpieces with differing ports are lined up next to the shanks. Because each piece is handmade, Ray can create 8,500 different bits to fit a customer’s needs.
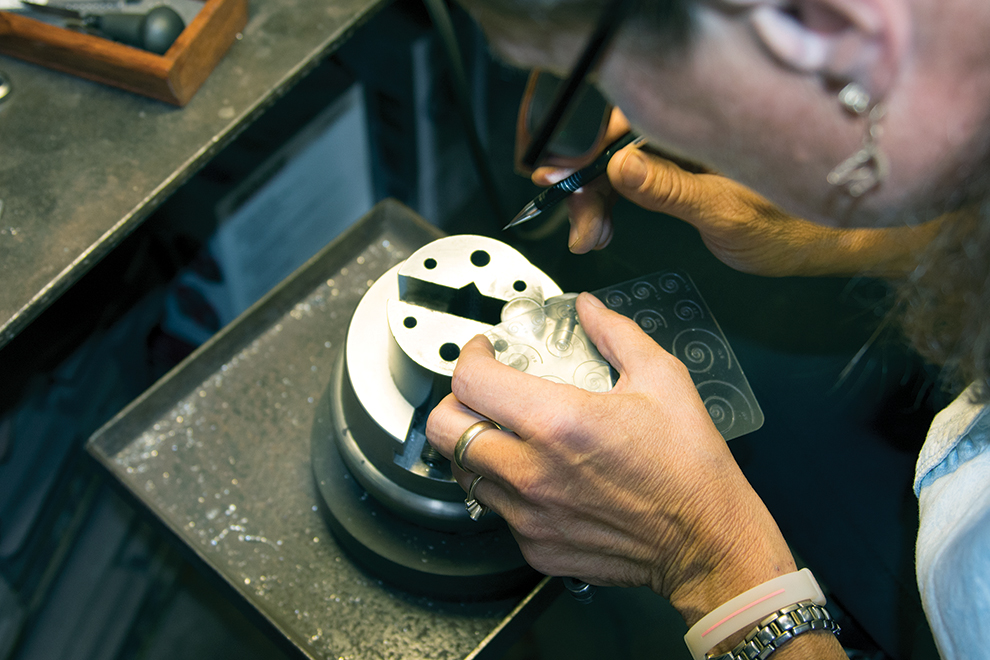
It’s easier to demonstrate the work process than explain it, Ray said as he walked to the shop entrance. Just a few steps inside the door, a standard bandsaw is affixed to the workbench. To any machinist, carpenter or do-it-yourselfer, it looks like your average bandsaw. But it isn’t precise enough for Ray’s work. Instead, he has made a jig that allows him to repeatedly and accurately cut each piece of steel. He has one for mouthpieces, one for shanks and another for spur parts.
“You can’t take a ruler and mark the length,” he said. “The thickness of that line can vary up to a 1/16 of an inch. This is the stop (jig) I’ve made. It goes up against every piece we’re going to cut so each cut is exact and quick.”
Even though he knows his stop is adjusted to just the right spacing, he doesn’t cut more until he’s measured it to be sure. Once he’s confirmed it’s perfect, he cuts enough for the day’s workflow, it could be up to 50.
“Feel that?” he asked. “Feel that sharp spur on both ends? We have to sand that smooth before we do anything else.”
He turns his back on the bandsaw and takes a few steps to a sander, flips the switch and the belt begins vibrating. He holds one end up to the abrasive sandpaper and then another and dips the hot metal into a bucket of water to cool it.
“Now feel that,” he said. “Feel how smooth that is?”
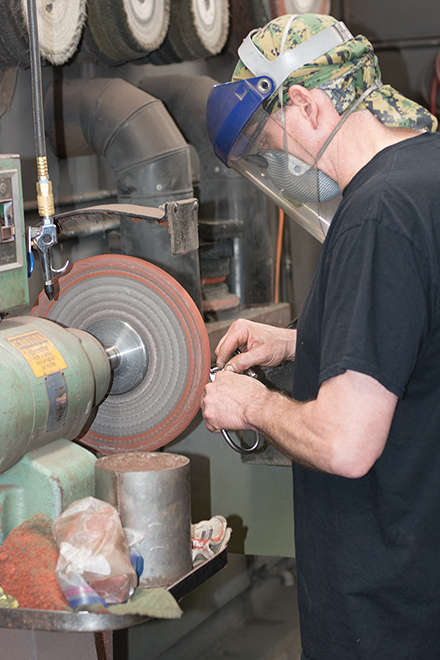
He moves a few paces to his left, around the end of a workbench and approaches a hip-height metal wheel about the size of a bistro table. The top is riddled with holes. This, he explains is a dichro bender, a specialized tool that forms precise curves on metal. Depending on what he’s making, a mouthpiece or the shanks of a bit, one piece of metal may be shaped as many as three different times.
“Ray knows a lot about bits, their leverage and how they feel in a horse’s mouth,” said Jay Starnes, a Summerton, South Carolina trainer. “When we’ve had him make custom bits for us, I’m able to tell him what I’m looking for when I’m using it on a horse and he goes from there.”
From here, Maheu moves a few steps to the welder. It’s time to tack on the rings that hold headstall and the reins. Depending on the piece, Candy jumps into the workflow – she does all the engraving that makes each piece distinctive. Originally, the work was outsourced to a local engraver. About seven years ago, Candy, a graphite and colored pencil artist, wanted to learn. Metal presented a new canvas to challenge her artistic skills. She uses stencils to sketch the basic design and free hands the rest.
“I had to learn to cut through my mistakes,” she said. “I had one bit where I made a mistake on the first shank. I took a picture with my phone and duplicated the design on the other shank so it matched. No one knew there was a mistake in it.”
She operates an air-powered engraving machine with a pedal, similar to that on a sewing machine. The engraver provides the pressure it takes to make each cut while saving the strain on her wrists. But the artwork, each flower petal, every scroll and the zig-zag pattern around the edge is all done by hand. Stencils help begin the design, but engraving is an art that takes skill and natural ability.
It’s difficult to estimate the time it takes to build a complete bit, because it’s a multi-day process. He may start with the mouthpieces, then move onto the shanks. Adding copper inlay to the mouth piece is time consuming. After the port is shaped, grooves are sliced into the steel – using another custom jig – he takes a seat and hunches over an anvil to pound each piece of copper into place.
“Our bits are so accurate because we have a process set up for knowing exactly where to cut,” he said. “When you’re welding the tail gate on a dump truck and you’re off an 1/8 inch it’s not going to matter. An 1/8-inch off on a bit is going to matter.”

Ray says that anyone who can read a ruler and use a square, can build bits, it’s not that hard. He’s just being modest. He’s naturally mechanically inclined and he has decades of metalworking experience. As a high school student, Ray attended the Chicopee Comprehensive High School where he was enrolled in the school’s welding program. When he graduated in 1966, he earned his high school diploma and a welding certification. He interned for a construction company, who hired him full time. Then he worked for a welding company and a welder’s union.
He started riding horses and continued and competing in gymkhanas through his early 20s. In 1973, a New York based barrel racer convinced Ray to relocate and hired him to train horses. After a few years, Ray went out on his own, but the ups and downs of the business convinced him to return to welding.
He went to work for an aircraft manufacturing plant and kept his own horses, eventually switching to Reining the and now Cutting. A hay delivery to Grand Prix show jumping trainer Jay Shuttleworth’s barn changed Ray’s professional path again. Shuttleworth was impressed by the trailer Ray used to haul hay and asked where he could find one.
“I told him I built it myself,” Ray said. “Then he asked me if I could build him some bits.”
His mechanical mind, knowledge as a horseman and experience fitting small parts for the aircraft plant was a trifecta. In the spring of 1978, he made an English D-ring bit for Shuttleworth and that spurred the beginning of a new chapter in his career.
Since then his bits have been used in virtually every discipline. Olympians McLain Ward and Lisa Howard use them on their jumping horses. Cutting horse trainer Tracy Barton has won nearly half his $2.5 lifetime earnings using a bit Ray designed for him. Western pleasure trainers like Starnes, Gil Galyean and Randy Wilson have all used one or more of his bits.
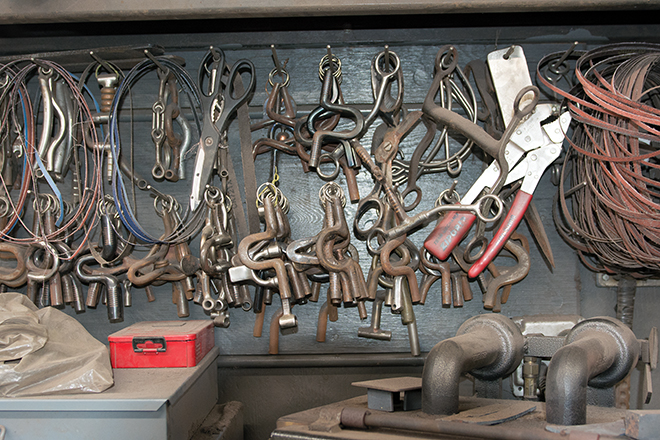
“I use one of his bits with a medium shank that’s pretty simple, but how the mouthpiece sits in the horse’s mouth is just a little different and it’s worked well,” Wilson said. “His stuff is high quality and very attractive.”
The sheer volume of work is too much for one person to handle and Ray has surrounded himself with equally talented craftsman. Parthemore is one of two employees and his craftsmanship matches Ray’s. Last year, Parthemore appeared on the History Channel’s “Forged In Fire” invitational tournament.
He’s been a metal worker since leaving the Marine Corps in 1980, becoming a welder and later evolving into blacksmithing and forging. Aside from building bits and spurs, he has made all types of things from a garden gate to a tomahawk. But he’d never made a curved Samurai sword known as a flamberge rapier, until the show gave him five days to do it – in front of cameras – winning the $50,000 grand prize.
“I couldn’t have done it without Ray’s support,” Parthemore said. “He was so supportive in encouraging me to do it and giving me the time off to participate.”
It takes months to prepare for shows, like the All-American Quarter Horse Congress. He’ll bring more than 500 bits and spurs to the Congress so customers have enough selection to choose from. Most will be wrapped in Crown Royal pouches and packed in 1980s suitcases to protect them during transportation. His most loyal customers know, he’s always accepting donations of those purple velvet pouches.

“I’ve had a lot of people save and drop those off for me,” he said laughing. “Just in case people are wondering, I didn’t drink all that Crown Royal myself.”
Building an inventory for Congress is only the beginning of the busy season. While there, they’ll take custom orders that will be completed in time to arrive under customer’s Christmas trees. Personalized orders are one reason, he’ll have fewer spurs than bits on display.
“People will buy bits off the rack, but when it comes to spurs most want a custom pair,” he said. “I’ll take enough for those who want to shop off the rack and to give others an idea of how they can customize their spurs with lettering and other designs.”
Rasp spurs, those made from a farrier’s rasp, are currently trendy. The file texture is distinctive leaving less room for personalization, though riders can choose upgrades like silver inlay in the neck and/or rowels and engraving on the buttons that snap into the straps. His shop can produce a pair of spurs in less than five hours, but it can take an hour and a half to add copper or silver inlay to a rowel.
One thing Ray most enjoys is trying a new design and seeing how the finished product turns out. He has plenty of spurs to choose from, but says he has two pairs right now that are a favorite. The first has a woman’s leg stretching from the band into the neck. The other, is a spur decorated with the symbols from playing cards. Where the neck meets the band, there’s a built-in bottle opener.
“This is my neck design here,” he said. “There’s been other spurs with bottle openers, but not with this design.”
“I can change out the rowels so if I’m riding colts, I can put on a duller one or if I’m riding an older horse with numb sides, I can put on a rowel with a little more,” Wilson said. “It takes about five minutes to change them out and I’m good to go.”
The price tag hanging from Ray’s spurs and bits start well into the few hundred dollars. But when you see the attention to detail and handwork that goes into each piece, it’s worth the investment.
“He knows a lot about what he does and the stuff is such good quality,” Starnes said. “Plus, he makes it a fun process.”
You must be logged in to post a comment Login